This study was a part of the Ph.D. dissertation titled (Development of Oil Well Cement Formulations for CO2-Rich Environment Relevant to Geologic Carbon Sequestration). The research was conducted by Mr. Ahmed Abdulhamid Mahmoud (Ph.D. Candidate) under the supervision of Dr. Salaheldin Elkatatny (Associate Professor at Petroleum Department, CPG).
In this study, modified montmorillonite nanoclay was used as a complementary additive to cement slurry prepared as a mixture of Saudi Class G oil well cement and other primary additives such as expandable material, fluid loss controller, friction reducer, and defoamer. The nanoclay particles were added to the cement slury to improve its resistance to the carbonation process when the cement matrix is attached by CO2 saturated brine.
The nanoclay particles were used because their interaction with the portlandite (Ca(OH)2) during the hydration process leads to production of more stable cement hydrate products in form of calcium-silicate-hydrates (C-S-H) which could effectively improve the cement resistance to carbonation process (Mahmoud et al., 2018), The x-ray diffraction (XRD) results of Figure 1 indicates that the concentration of the portlandite is low for the sample with nanoclay.
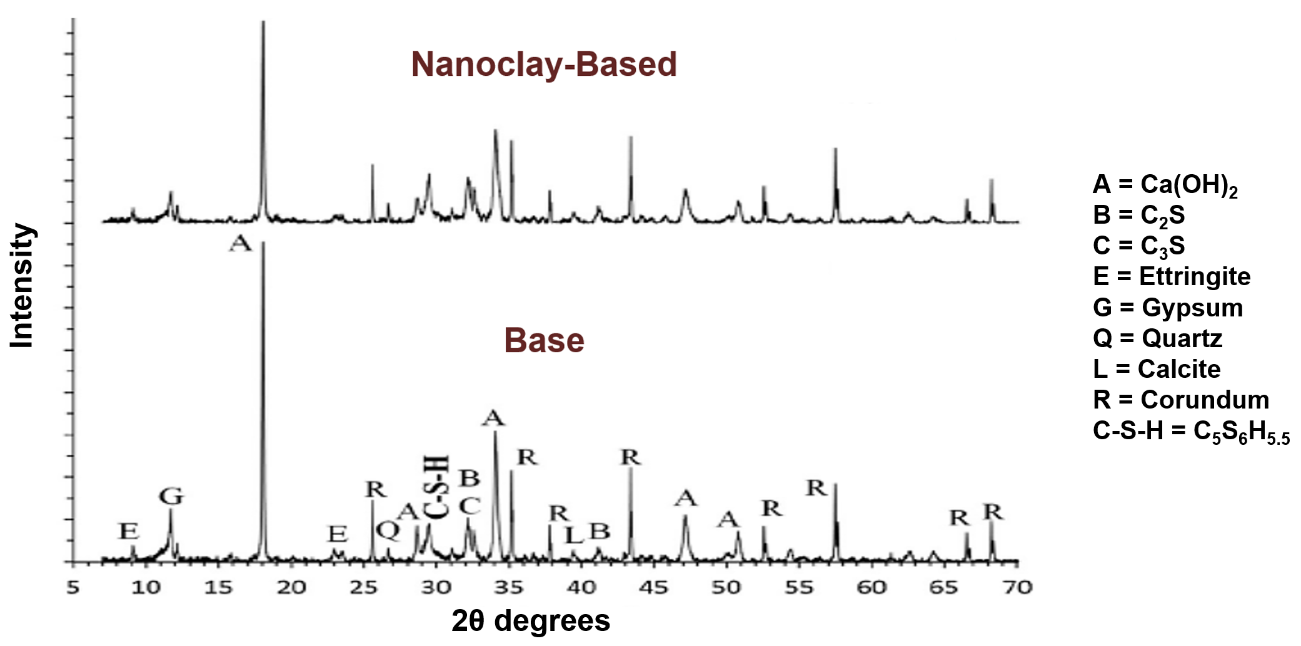
Figure 1. The XRD patterns for the base and nanoclay-based cement samples.
Figure 2 shows the computed tomography (CT) scan and real-core images for the base and nanoclay-based samples, this figure dominates that for the CT scan images at every slice there is a change in the density of the sample along its diameter for both the base and nanoclay-based cement. The region in the dark orange color of the CT scan images in Figure 2 indicates the intact region which did not attack by the acidic brine, while the remaining outside regions (light orange and light green regions) are the altered regions which attacked by the CO2-saturated brine. Comparing the CT scan images for the base and nanoclay-based cement indicates that the carbonated depth (attacked region) inside the nanoclay-based cement is less than that for the base cement as indicated by the small thickness of the light orange and green regions of the nanoclay-based sample compared to the base sample. The real core samples in Figure 2 also confirm the results of the CT scan which showed that the altered region in case of the nanoclay-based sample is considerably less than that of the base sample.
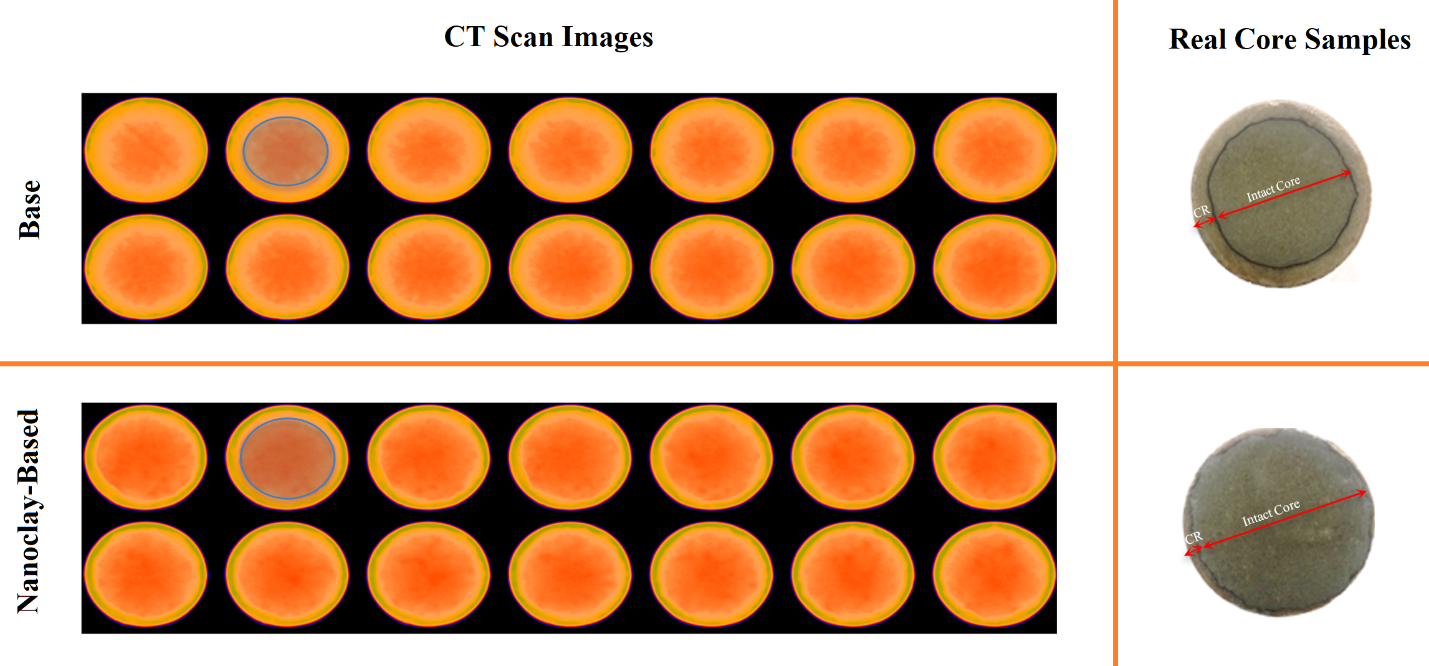
Figure 2. The CT scan images and real core samples of the base and nanoclay-based cement samples exposed to CO2-saturated brine at 95 °C and 10 MPa for 30 days (Mahmoud and Elkatatny, 2019).
The team at CPG includes Dr. Salaheldin Elkatatny and Mr. Ahmed Abdulhamid Mahmoud.
References:
- Mahmoud, A.A., Elkatatny, S., Ahmed, S.A., Gajbhiye, R., (2019). Influence of Nanoclay Content on Cement Matrix for Oil Wells Subjected to Cyclic Steam Injection. Materials 12(9), 1452; https://doi.org/10.3390/ma12091452.
- Mahmoud, A.A., and Elkatatny, S., and Mahmoud, M., (2018). Improving Class G Cement Carbonation Resistance Using Nanoclay Particles for Geologic Carbon Sequestration Applications. Paper SPE-192901-MS Presented at the 2018 Abu Dhabi International Petroleum Exhibition & Conference, Abu Dhabi, UAE, 12-15 November. https://doi.org/10.2118/192901-MS.