The current Gas-Oil-Separation-Plant (GOSP) operation practice is to set the parameter determined at the design stage based on a simple laboratory test. It does not account for the changes in operation parameters resulting in less liquid recovery and profitability loss. The objective of this study, conducted by CPG faculty Dr. Rahul and his research team, was to optimize the GOSP operation to maximize the oil recovery in an integrated framework of GOSP operation and develop adoptive system for GOSP operation irrespective of drifts in plant parameters.
A typical GOSP plant was considered as a candidate for the project as shown in Figure 1. A dynamic simulator “OmegaLand” were utilized to mimic the GOSP plant. During the process, the data from the initial PVT analysis were considered as an input for the process simulator. The simulations were performed to evaluate the effect of various process variables such as pressure, temperature, number of stages considering a Reid vapour pressure on the oil recovery. The optimization was carried out for the process variables using Artificial Intelligence (AI) techniques and the results from simulations were analysed to obtain maximum oil recovery.
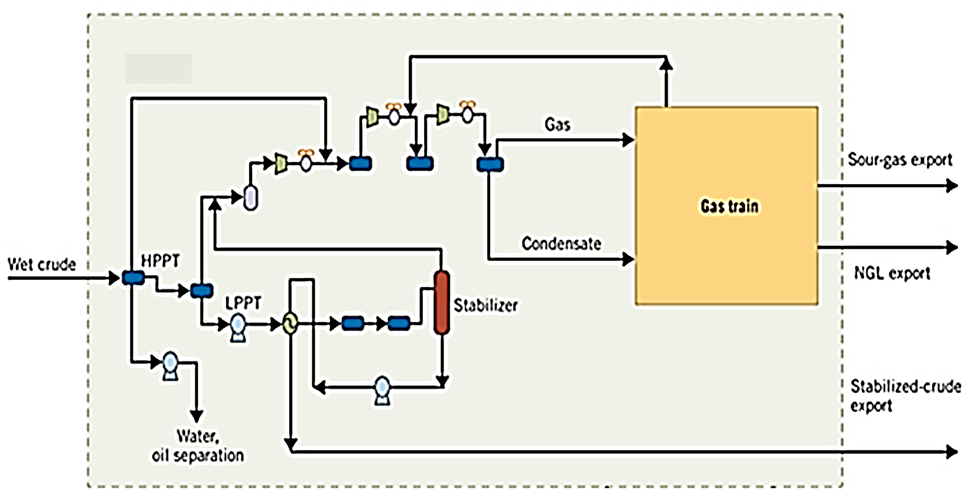
Figure 1. A typical gas-oil-separation-plant process (Amminudin, 2010)
Process Optimization
For the optimization process the data were generated by fixing the stabilizer pressure at one value (55 psi) and fixing the ambient temperature at specific value. The OmegaLand GOSP model were runs at all the range of LPPT pressure until the model reaches the steady-state at each run, then move to the next ambient temperature and run the model for all LPPT pressure range until the model reaches the steady-state condition. This way used for all ambient temperature range. The increment of ambient temperature is (2oC) and LPPT pressure is (2 psi) in every step. The output data generated by the model is utilized to find an optimum condition at which the maximum oil recovery can be obtained from the production facility in an efficient and economical way.
As shown in Figure 2, the oil recovery is plotted as a function of LPPT pressure for the entire range of temperature (15 to 41 oC) considered in this study. The stabilizer pressure is kept constant at 55 psi. It can be observed that for constant temperature there is an optimum value of the LPPT pressure at which maximum liquid recovery can be obtained for a given feed and operating condition.
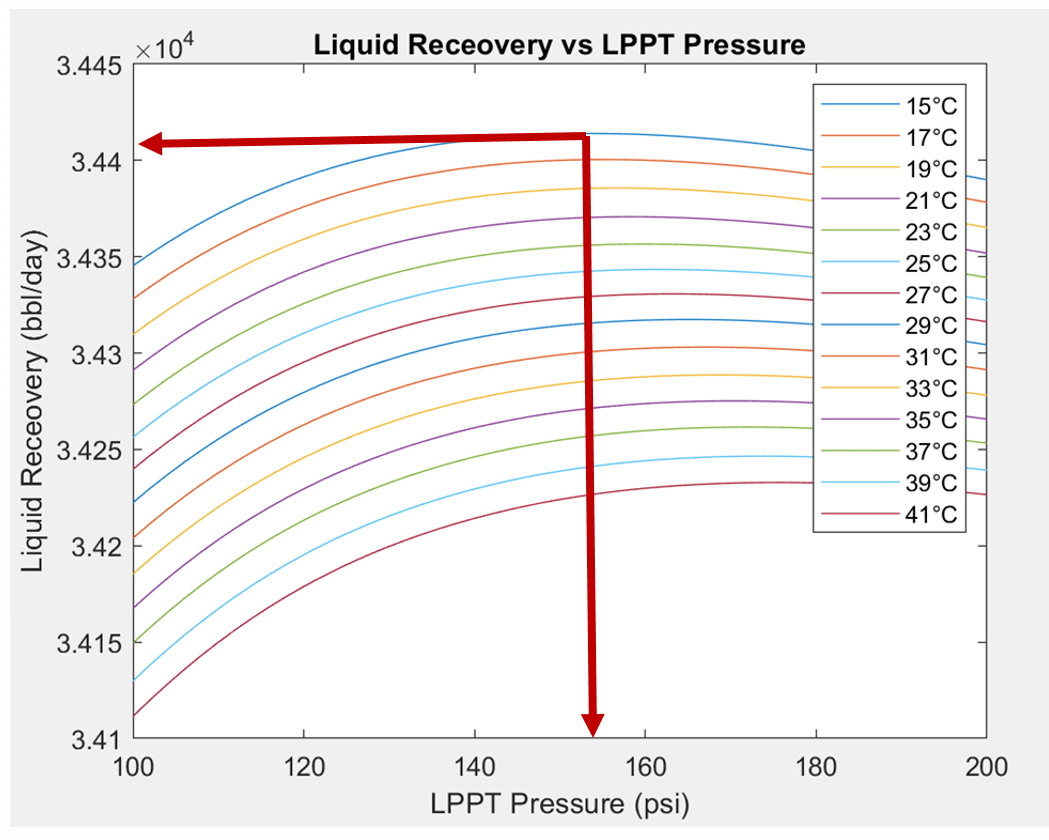
Figure 2: LPPT pressure and Oil recovery as a function of temperature
In addition, it can be seen from Figure 3, that the liquid recovery is significantly affected by the temperature, for low-temperature 15oC corresponds to night or temperature in the winter, higher recovery can be obtained by optimizing the pressure of the system. Similarly, at high-temperature 37oC corresponds to day or temperature in the summer, the liquid recovery is lower which can increase by setting the optimum pressure condition.
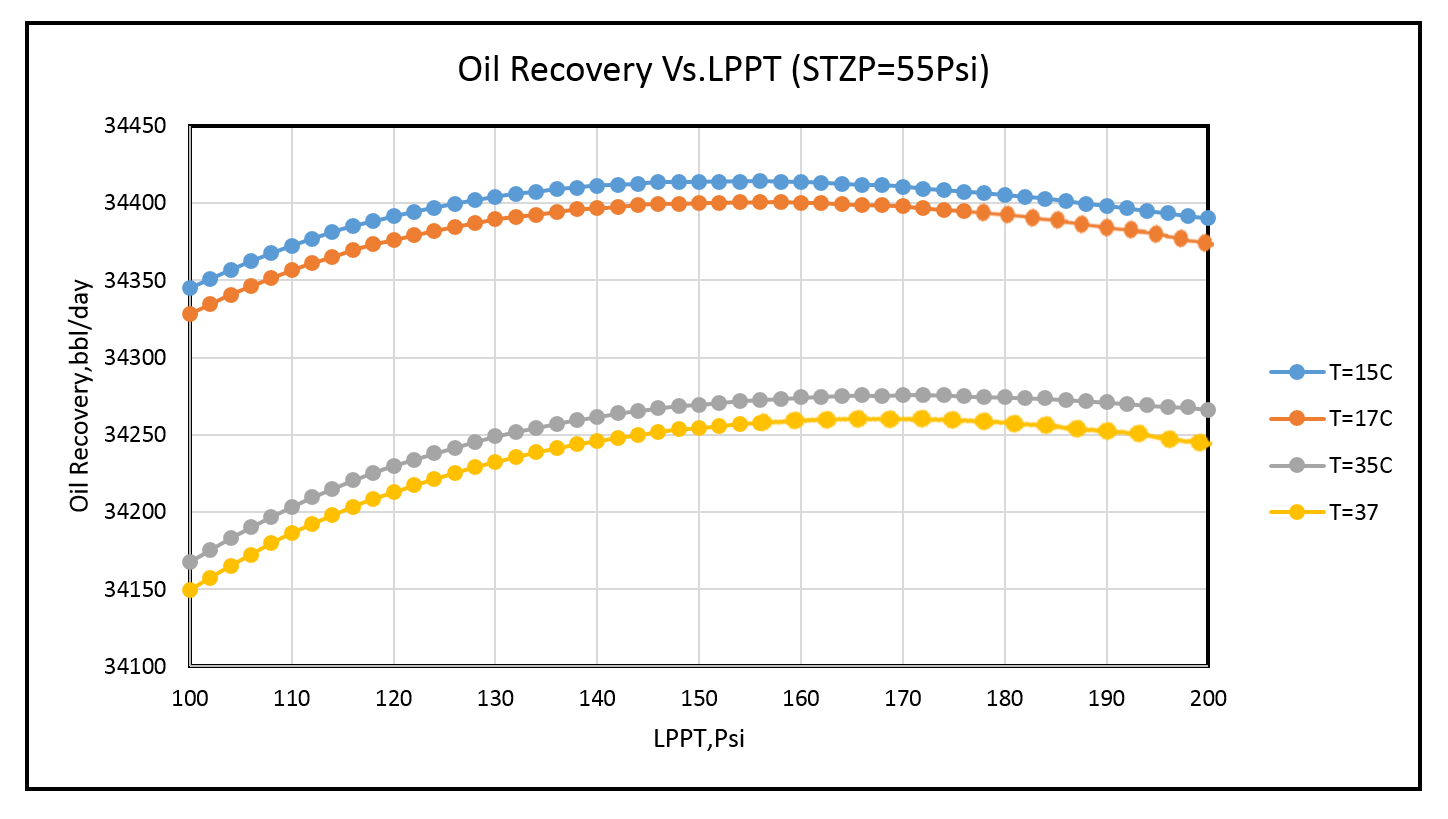
Figure 3: Effect of temperature (day/night or summer/winter) on liquid recovery
Operation Decision Support System (ODSS)
The results show that liquid recovery is highly affected by the variation in temperature. The effect of change in temperature can be compensated by adjusting the LPPT pressure to an optimum value which can maximize the liquid recovery of the GOSP. The optimized parameters can be adjusted by developing the Operation Decision Support System (ODSS) which can control and achieve the optimum pressure according to the variation in temperature. The conceptual model of the ODSS is shown in Figure 4.
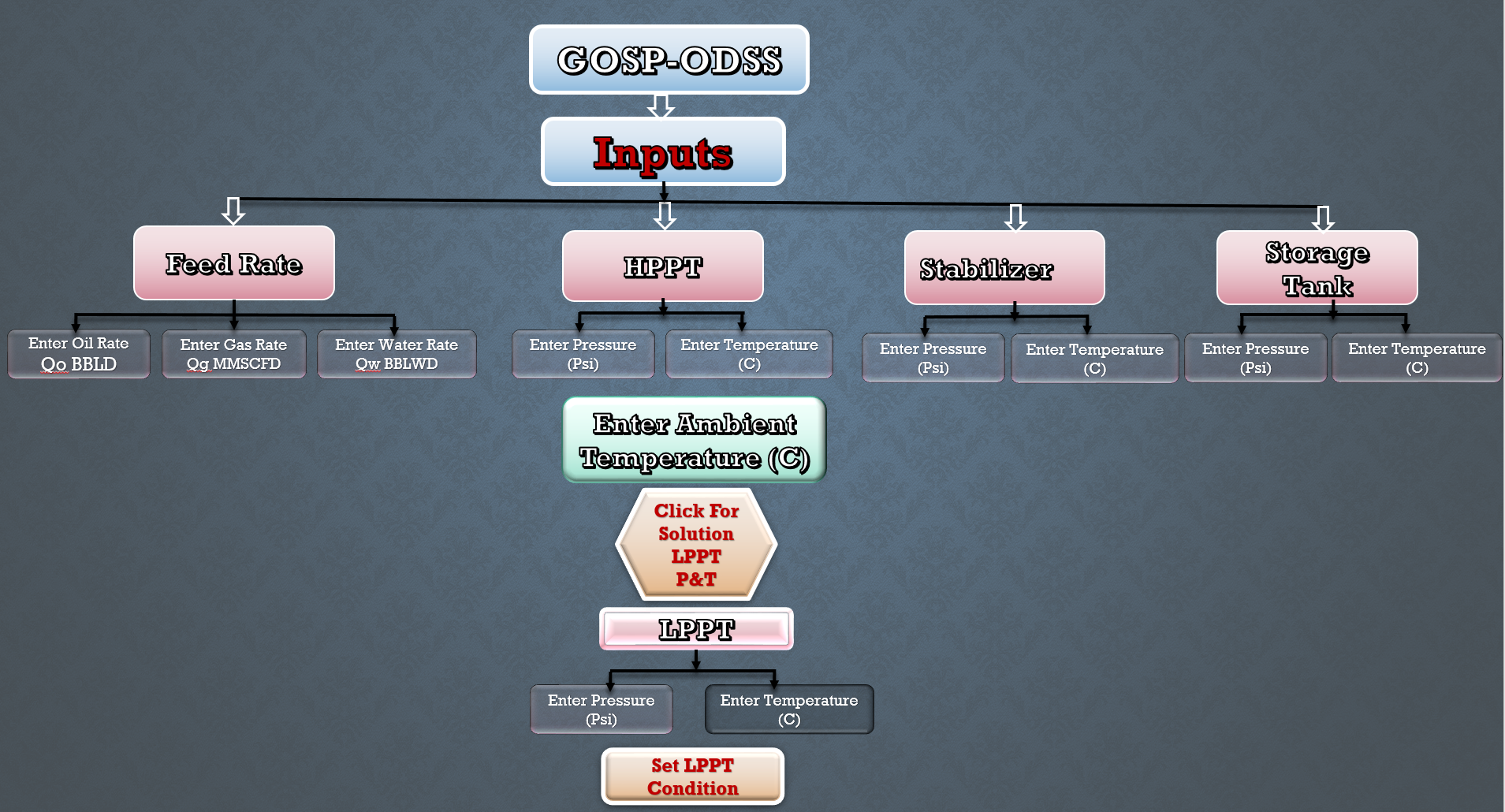
Figure 4: Conceptual model of Operation Decision Support System (ODSS)
The decision support system requires input such as feed rates of oil, water, and gas. This data is available from the field. Along with the feed data system inputs such as HPHT P&T, stabilizer P&T, and storage tank operating condition is required for the ODSS. Once the constant input parameters were fed to the system. The ODSS system will determine the optimum pressure of LPPT to get maximum liquid recovery for the corresponding ambient temperature.
The result shows that optimization of the GOSP plant is very a complex process. The simulation indicates small variation in the operation completely destabilized the process and requires long time to stabilize again. There are many parameters, which affect the operation process and oil recovery of the GOSP plant. Pressure and temperature have significant impact on oil recovery and control system must be implement for maximizing oil recovery and minimizing the drift in GOSP operation. The Artificial Intelligence appears to be best optimization tools as due to different units and their governing principles in an integrated framework of GOPS plant.
This study addresses the shortfall of the current practice of GOSP optimization process. The new method maximizes the oil recovery by optimizing the parameter of the complete process taking into account the interconnectivity of the units irrespective of drifts in plant parameters and changes in the reservoir oil composition. The method shows a way to maximize the value of resource through process improvement and enhanced production efficiencies while supporting integration across the hydrocarbon value chain.
This research project is under collaboration with YOKOGAWA, KSA. The team members include Dr. Rahul Gajhiye, Dr. Mohamed Mahmoud, and Ala Al-Dogail (CPG, KFUPM) and Dr. Mustafa Al-Naser and Abdullatif Alnajim (YOKOGAWA, Saudi Arabia).
References:
- Al-Dossary, B., AL-Naser, M., Al-Dogail, A., Gajbhiye, R., Al-Qathmi, A., & Mahmoud, M. (2020, January 13). Decision Support System for Optimizing GOSP Operation. International Petroleum Technology Conference. doi:10.2523/IPTC-20021